I carried out computational fluid dynamics (CFD) modelling of the combustion process in a gas stove for Yeoman Stoves. This company constructs domestic gas stoves and originated the ‘balanced flue’ design which virtually eliminates the risk of carbon monoxide poisoning and increases efficiency. In a conventional design combustion actually causes cold air to be drawn into the building, in the least efficient designs this can actually result in a net cooling effect to the building as a whole!
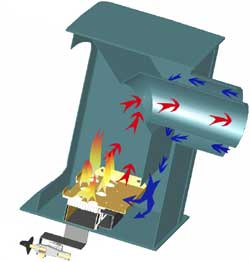
The combustion chamber is sealed from the room. Cold air is drawn from outside via the outer ring in the flue.
Despite the balanced flue design having a number of advantages general acceptance by the public had been limited due to the necessity to install an expensive and unsightly right angled flue on the outside of the building. My brief was to improve the efficiency of the design so that a simple strait flue could be used.
Mathematical Modeling
Combustion efficiency was improved by first considering the fundamental nature of the buoyancy driven flow, combustion and heat transfer. A complex mathematical relationship was established for the whole combustion process and an Excel model was created.
The process was simulated to determine certain unknown heat transfer coefficients. This involved creating a reliable mesh with over 140,000 elements volume elements; a mixture of Tet and Hex regions. Considerable effort was required to produce a mesh capable of reliably modeling the heat transfer coefficients of the surfaces containing the combusting gas while minimizing computational expense.
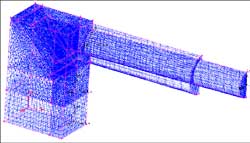
Coefficients were then incorporated into the mathematical model with variable parameters adjusted to optimize the combustion process. The optimized design was verified again using experimental results.
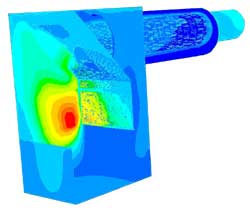
Design for Manufacture
Considering the existing production process the required changes were developed into a design for manufacture. A prototype was constructed by Yeoman Stoves and this was then tested.
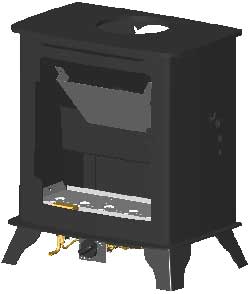
The design allows a far simpler flue while improving combustion efficiency. Production costs for the complete product were reduced by 10%.
Great article! Your site and blog are really brilliant and the information is super useful. Thank you; we’ll put it to work. Keep sharing with us.